Tungsten Copper CIP
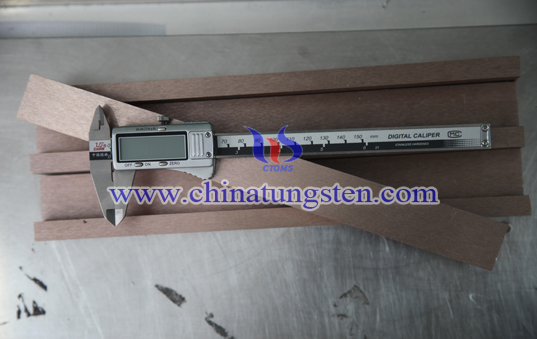
Introduction
Cold Isostatic Pressing, CIP, it refers to the isostatic pressing technique carried out at the room temperature. CIP usually uses rubber and plastics as mold wrapped materials, the liquid as the medium, the pressure is 100-630MPa, which mainly applied in powder molding. The purpose is to provide a sintered preform for the next process, such as forging or HIP process and so on. Compared with common molding process, tungsten copper CIP process has more uniform compacts and higher efficiency.
Process
According to different pressure transmission fluid, including cold isostatic wet-bag method and the dry bag method isostatic pressing and soft mode. Wet-bag method is put the installed mold directly into the fluid pressure medium, contact with the liquid and then press molding. This method can be changed to any shape and size of the elastic mold, products great flexibility, but every time bagging, bags unloading operations, processes are more difficult to improve efficiency. Isostatic dry bag method is a "double bag" system, consisting of a "product bag" (inner mold) and a "main bag" (pressurized main mold) components. After the "main bag" first fixed in the cylinder, do not remove the work, the powder into another "product bag", and then put inside the "main bag" pressure, after forming the piston out of the cylinder. Throughout the process the bag is not in contact with the product with the liquid, it suitable for continous operation and mass production, but the main pressurized module can not be changed frequently and the product specification is limited.
Advantages
There is certain friction between powder grains, powder and punch, and mold wall of conventional molding process, which pressing force distribution and transmission of certain changes occur, and also resulted in various parts of the compact density and intensity distribute uneven; By comparison, CIP process has more uniform molding process, and it can ensure that the compact has uniform density and net shape, low consumption of molding tool and high molding efficiency.